Voltage Balance and real world effects
Phase Perfect® vs other phase conversion solutions
When reading the marketing literature of various single-phase to three-phase converters you will quickly see a theme emerge surrounding voltage balance. The reason so much attention is focused on unbalanced voltage is because it ends up being the most important factor when it comes to efficiency, power output, reliability, and longevity of the entire system.
Simplified breakdown of how well phase converters are able to maintain voltage balance
Permanent imbalance while running.
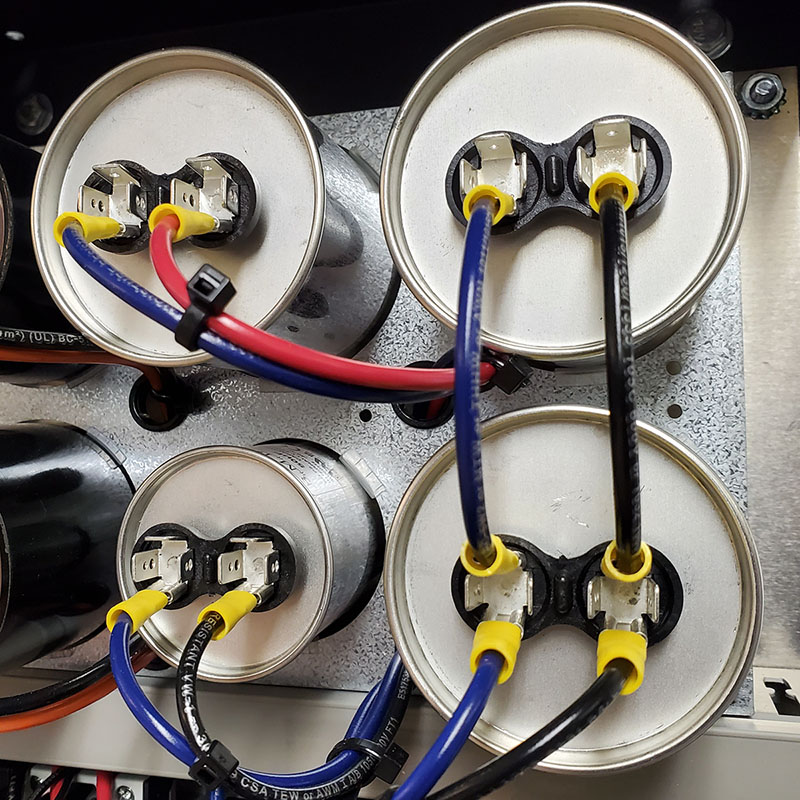
Only provides near-optimal voltage balance within a narrow operating window.
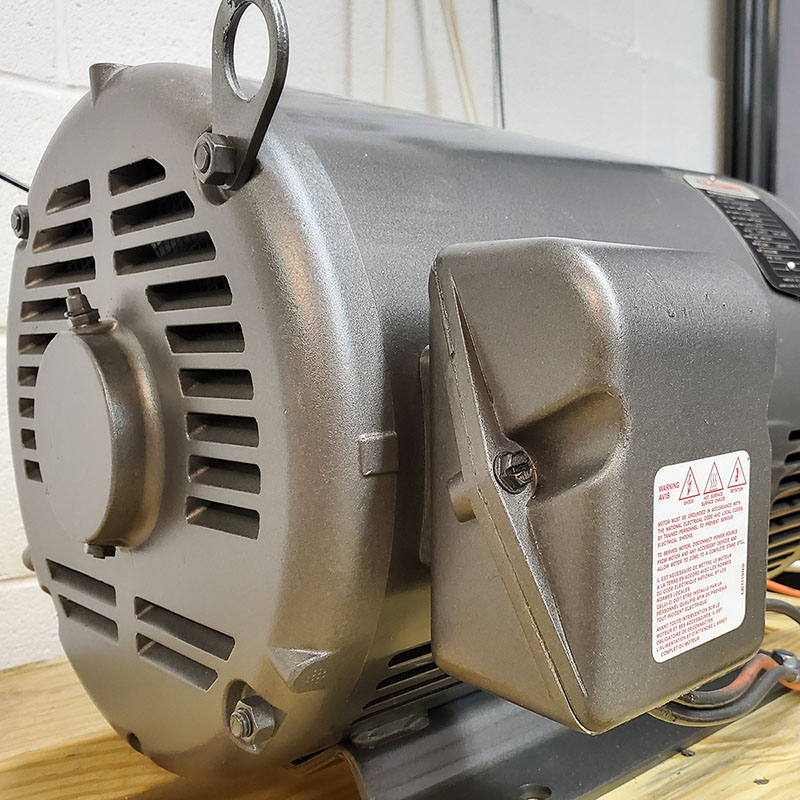
Computer controlled to maintain optimal voltage balance at all times.
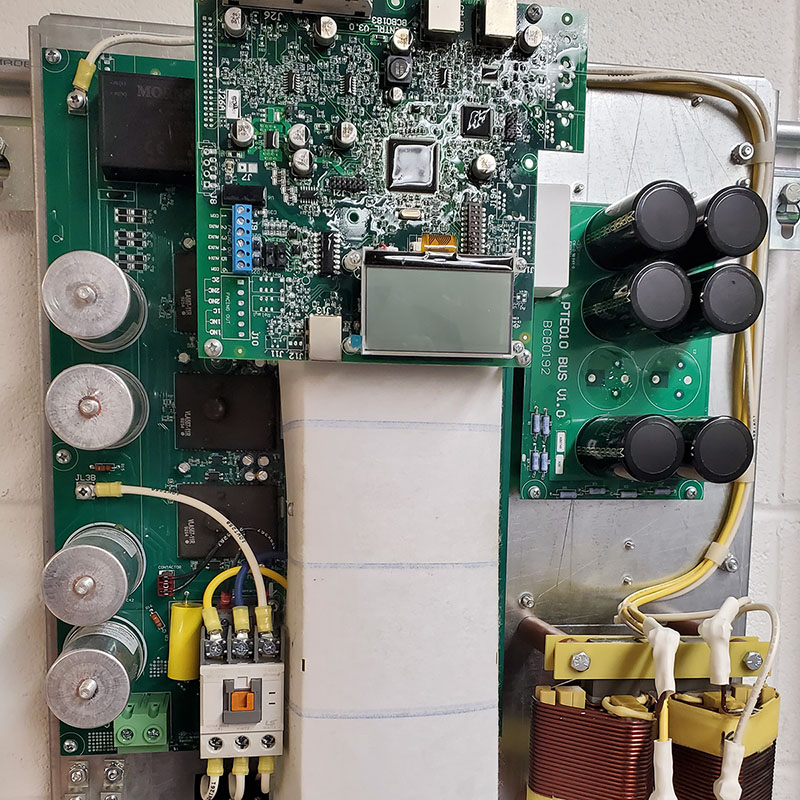
Let’s look a bit more in-depth at why voltage balance is so important...
“When the line voltages applied to a polyphase induction motor are not equal, unbalanced currents in the stator windings will result. A small percentage voltage unbalance will result in a much larger percentage current unbalance. Consequently, the temperature rise of the motor operating at a particular load and percentage voltage unbalance will be greater than for the motor operating under the same conditions with balanced voltages.”
This is actually reasonably clear (for a technical standards document): balanced voltage good, unbalanced voltage not good. But what does this mean for the motor of your conveyor, grinder, saw, dust collector, lathe, or whatever your three-phase load might be?
In the face of unbalanced voltage (phase-to-phase), a flux is produced in the air gap between the rotor and stator that works against the rotation of the rotor. Even a small amount of voltage unbalance can cause excessive increases in current. Excessive current means excessive heat.
Ok, rotary and static phase converters will make a little more heat in my motor.
What’s the big deal?
How much heat are we talking here?
What is the real-world effect of not having balanced voltage?
FIRST Motor winding insulation
% Voltage Unbalance | Winding Temp (C) | Winding Temp (F) | Expected Motor Life (Years) |
---|---|---|---|
0% | 120 | 248 | 4.5 |
1% | 122 | 252 | 4+ |
2% | 128 | 262 | 2.5 |
3% | 138 | 280 | 1.5 |
4% | 152 | 306 | 0.5 |
5% | 170 | 338 | 0.17 (2 Months) |
The temperature of the windings will increase by approximately twice the percent of voltage unbalance squared.
2 x (% UNBALANCE)^2 = Degrees C winding temperature increase
Motors with Class B insulation (the most common insulation type in the United States) should have an insulation life of 20,000 hours (about 2.25 years) at the maximum allowable operating temperature of 130 C, which is based around operating with a 2% unbalance.
As you can see in the table of expected motor life, a significant voltage unbalance could regularly bring the motor(s) in your equipment to end-of-life, even at only hobby-level usage.
Expected motor life (in years) based on continuous-duty, 24/7-usage.
SECOND Grease-packed/greasable bearings
Many industrial greases have a useful life or re-grease interval of 40,000 hours (4.5 years) when operated within a normal industrial range of about 40-70 C (104-158 F) and modest speed and/or load.
The life of the grease can drop to as low as a few weeks at operating temperatures of 170 C (338 F). Under these conditions it would take an extremely rigorous maintenance schedule to stay ahead of the degradation of the grease in the bearings.
Environmental factors certainly apply, but the heat transmitted to the bearings in a motor is directly proportional to the heat generated by the motor windings.
Real-world effect: heat destroys motors
The failure modes of induction motors are most often the bearings or motor winding insulation. The expected life span of both bearings and windings are driven quite dramatically by heat. Not only that, both bearings and motor windings deteriorate in the same temperature range because both the winding insulation material and the grease in the bearings are derived from petroleum. High temperatures in these petroleum-based materials causes oxidation, and the rate of oxidation doubles for every 10 C increase in temperature. As a direct consequence, the life of motor winding insulation and grease in motor bearings is cut in half for every 10 C (18 F) increase in temperature.
Motor Starting Ability
Phase converters have wildly different characteristics on their ability to start and run motor loads.
Read MoreDefinitions
Common terms related to phase conversion technology used throughout this website and across the internet.
Read MoreSizing A Phase Converter
Oversizing, or splitting across multiple units, learn how to best accommodate available incoming power.
Read MoreThese pages contain comparisons of phase conversion technologies, including static, rotary, and digital phase conversion, applied to simple and complex scenarios.
Phase Perfect® provides uncommon value in Phase Conversion Technology
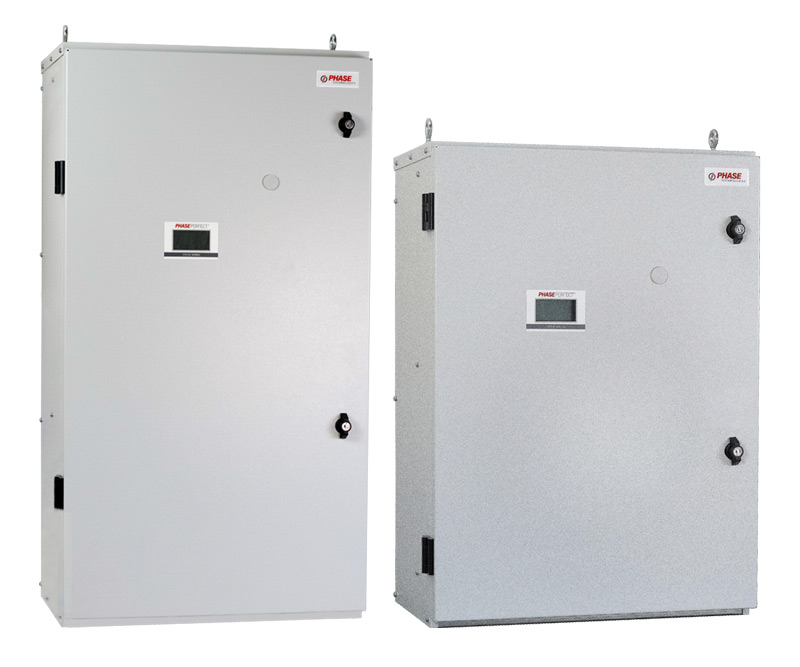
The original Phase Perfect® supplies power to some of the most demanding applications available under some of the most challenging conditions imaginable. Utility-quality three-phase power anywhere you need it.
See the Phase Perfect®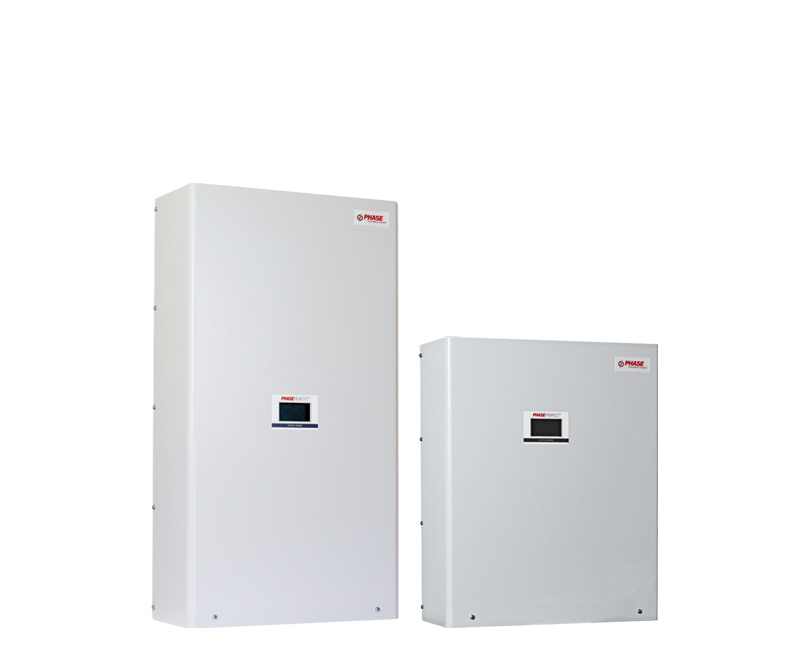
The Phase Perfect® is also available in a compact, high-value, configuration where the customization options of the original are not required. These Enterprise models have the same modern digital phase conversion technology inside as the original.
See the Phase Perfect® Enterprise